Centros de maquinado
- 1. Funciones y características principales
- 2. Surgimiento y desarrollo de centros de maquinado
- 3. Estructura general y tipos de centros de maquinado
- 4. Diferencias entre tipos horizontales y verticales
1. Funciones y características principales
Hoy en día, los centros de maquinado son ampliamente utilizados en los sitios de fabricación. Los centros de maquinado son equipos críticos para el maquinado de piezas y componentes metálicos, además de su objetivo principal de fabricación de matrices. Como ejemplo, los centros de maquinado en la industria del automóvil se utilizan para el rectificado y taladrado eficientes de las piezas del motor, así como para hacer matrices para los componentes de la carrocería. Muchos otros productos comúnmente utilizados en la vida diaria y en entornos industriales, se fabrican con centros de maquinado.
Los centros de maquinado cuentan con una función computarizada de cambio automático de herramienta. Generalmente, un operador debe intercambiar las herramientas en una máquina herramienta CN. En cambio, los centros de maquinado cuentan con un brazo de cambio que recupera e intercambia automáticamente las herramientas, desde un depósito de herramientas, donde se ubican durante el maquinado de las piezas. Esto ahorra tiempo y esfuerzo necesarios para los cambios de herramientas estándar y, en consecuencia, permite operaciones automatizadas y ahorradoras de energía, al mismo tiempo que se reducen los costos.
En los últimos años, la aparición de centros de maquinado de cinco ejes, equipados con dos ejes de rotación además de los tres ejes convencionales, ha permitido el maquinado de formas con una complejidad aún mayor.
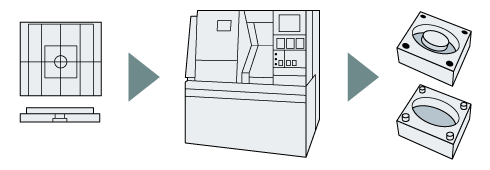
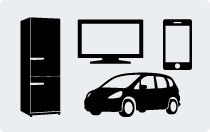
2. Surgimiento y desarrollo de centros de maquinado
La transformación de piezas metálicas generalmente incluye pulir superficies y ranuras, además de aplicar una serie de métodos de maquinado complejos como perforar, taladrar (agrandar orificios) y roscar. Convencionalmente, se utilizaban selectivamente diferentes herramientas de corte, como la fresadora, fresadora de extremo, taladros, herramientas de perforación y machuelos para estos procesos de maquinado.
Con la aparición de los tornos CN, poco después, se desarrolló una función de cambio de herramienta operada manualmente llamada torreta, lo que hizo que el cambio de herramientas de corte fuese más práctico. Los centros de maquinado llevaron esta idea un paso más adelante, a través de intercambios automatizados de herramienta, controlados por computadora. Los centros de maquinado pueden realizar continuamente varios tipos de maquinado al mismo tiempo en diferentes superficies de una pieza, lo que mejora en gran medida la eficiencia de producción. Incluso hoy en día, los centros de maquinado siguen mejorando con avances en la precisión y velocidad de maquinado, año tras año, lo que los convierte en una parte fundamental del proceso de fabricación.
Visite cualquier fábrica de metalurgia para ver una cantidad de centros de maquinado que trabajan incesantemente día tras día. Sólo se requieren unos pocos operadores en el sitio para monitorear las máquinas.
En los tornos CN, las herramientas están acopladas a una torreta, que se gira manualmente.
- A
- Torreta
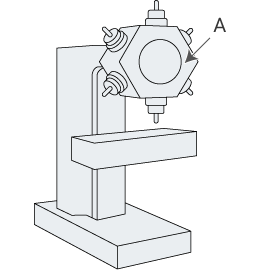
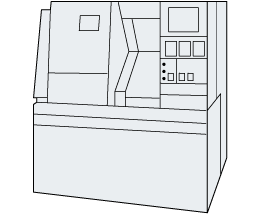
3. Estructura general y tipos de centros de maquinado
Los centros de maquinado pueden clasificarse ampliamente en tres tipos, según su estructura: horizontal, vertical y tipo pórtico. El tipo horizontal, el primero en desarrollarse, se puede definir simplemente como una máquina en la que el eje al que se une la herramienta de corte se monta horizontalmente (o paralelo al piso). En contraste, los tipos verticales tienen el husillo en posición vertical. Los tipos de pórtico, por otro lado, tienen una estructura en forma de puerta con el eje montado en el techo de la puerta, mirando hacia abajo.
Usando el tipo horizontal como ejemplo, la estructura general de un centro de maquinado consiste en una parte de base llamada cama en la parte inferior, una silla que se mueve sobre la cama, una mesa unida a la parte superior de la silla para colocar la materia bruta, una columna instalada perpendicularmente a la cama, y una cabeza de husillo donde se fijan las herramientas de corte.
4. Diferencias entre tipos horizontales y verticales
Los centros de maquinado horizontales tienen un husillo con una herramienta de corte montada, que sale lateralmente, y maquina las piezas en la dirección horizontal. La columna se mueve a lo largo del eje X, la silla a lo largo del eje Y, y la mesa a lo largo del eje Z. Esta combinación permite el maquinado tridimensional. Además, algunos modelos tienen un eje B que gira la mesa horizontalmente, lo que hace posible maquinar materiales utilizando un total de cuatro ejes.
Una ventaja de los tipos horizontales es la capacidad de mecanizar cuatro superficies de una pieza, cuando se utiliza un centro de mecanizado de cuatro ejes con un eje B, todo al mismo tiempo. Esto elimina la necesidad de que los operadores cambien manualmente los cuatro lados de la pieza y, por lo tanto, también contribuye a una mayor precisión de mecanizado. Además, el mecanizado desde la dirección horizontal permite que las virutas caigan, lo que ayuda a evitar que éstas se acumulen en la pieza de trabajo y se hundan en la cuchilla.
Contrariamente, los centros de maquinado vertical tienen el husillo en posición vertical y las piezas de trabajo se maquinan desde arriba. Generalmente, la mesa se desplaza horizontalmente sobre los ejes X y Y, y el eje se mueve verticalmente, permitiendo un maquinado triaxial.
En comparación con los tipos horizontales donde el eje está situado al lado de la pieza de trabajo, los tipos verticales ocupan menos espacio de instalación, lo que los convierte en una opción popular. Además, el maquinado desde arriba de la pieza de trabajo les permite a los operadores trabajar mientras comparan el maquinado con los dibujos de diseño. Sin embargo, el maquinado en la parte superior de la pieza de trabajo hace que las virutas se acumulen en la misma, creando la necesidad de un soplador que utilice aire comprimido, o de un enjuague con lubricante para eliminar las virutas de manera adecuada.
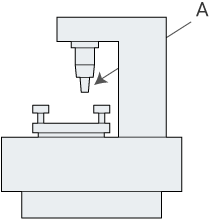
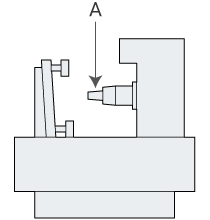
- A
- Husillo con herramienta acoplada